
Your Guide to Non Slip Industrial Flooring
Discover how to choose, install, and maintain the right non slip industrial flooring to boost safety and efficiency in your facility. A practical guide.
Don't think of non slip industrial flooring as just another maintenance cost. It’s a foundational investment in the safety, efficiency, and long-term health of your entire business. Slips, trips, and falls aren't minor issues; they're a leading cause of workplace injuries that lead to serious downtime, painful insurance claims, and a real dip in team morale. The right flooring turns a massive liability into one of your most strategic assets.
Why Your Facility Needs Non Slip Industrial Flooring
Picture your busiest warehouse floor. Now imagine it's just standard, slick concrete. Every little spill, every bit of moisture tracked in from outside, instantly turns that surface into a workplace ice rink. It's unpredictable and downright dangerous. Your team has to move cautiously, forklift operators need to be extra careful, and the threat of a costly accident hangs in the air all day, every day.
Now, let's swap that out for a professionally installed non-slip surface. Suddenly, that same floor is more like a high-performance track. It’s engineered to provide the grip and stability your people and machinery need to move with confidence, safety, and speed. This isn't just about ticking a compliance box; it's about building a fundamentally safer and more productive operation from the ground up.
The Bedrock of a Secure and Efficient Operation
When you get the flooring right, the benefits ripple out across the entire operation. A proper non slip industrial flooring system isn't just about preventing falls—it becomes the very bedrock of a secure and profitable business, directly impacting your bottom line in a few key ways.
A secure floor gives your team the confidence to perform at their best. When employees aren't subconsciously worried about navigating a slippery surface, they can focus 100% on their tasks. That confidence translates directly into better productivity and higher-quality work.
Real-World Example: A busy parcel distribution center switched to a textured epoxy flooring system in their main sorting area. The immediate benefit was a 90% reduction in slip-related incidents. But the unexpected benefit was a 15% increase in throughput. Why? Staff felt safer moving quickly between conveyor belts, which reduced hesitation and boosted overall operational speed.
A Strategic Advantage in a Growing Market
The worldwide push for better workplace safety isn't just a passing trend—it's becoming a global standard, and the market numbers prove it. The global non-slip flooring market is on track to grow from an estimated $15 billion in 2025 to a massive $25 billion by 2033. This surge is largely fueled by stricter safety regulations that demand high-traction surfaces to slash workplace accidents. For more on this, you can explore the full market research on datainsightsmarket.com. Investing now puts your facility ahead of the curve.
Here are the immediate, tangible benefits you can expect:
- Reduced Workplace Accidents: Drastically cut the risk of slips and falls, which are consistently among the most common and costly workplace injuries.
- Increased Productivity: Your team and equipment can move faster and more confidently, smoothing out your workflow and getting rid of bottlenecks.
- Lower Insurance Premiums: A proven track record of safety can lead to a real reduction in your workers' compensation insurance costs over time.
- Enhanced Employee Morale: When you invest in your team's safety, you're sending a clear message: you value them. That's a huge boost for morale and retention.
While a full flooring system is an incredibly powerful solution, you don't have to do it all at once. Targeted matting can provide an immediate and noticeable improvement in high-risk zones. For a closer look at this flexible approach, check out our guide on how to boost safety and productivity with industrial non-slip mats.
Decoding Your Non-Slip Flooring Options
Choosing the right material for your non-slip industrial flooring can feel like a high-stakes decision. With so many options out there, it’s easy to get lost in a sea of technical jargon. Think of this section as your personal flooring consultant—we're going to move beyond a simple list and dig into the "why" behind each choice so you can match the perfect material to your facility's real-world demands.
The most common solutions you'll run into are specialized coatings and treatments engineered to create tough, high-traction surfaces. Let’s break down the top contenders and see where each one truly shines.
Epoxy Coatings: The Versatile Workhorse
Epoxy is a resinous coating that chemically bonds with concrete to create a hard, durable, and often seamless surface. It's like giving your floor a protective, high-performance shield. Its biggest strength is its incredible versatility and knack for shrugging off impacts.
But here’s the catch: not all epoxies are created equal. A standard, smooth epoxy coating can become dangerously slippery when wet, which completely defeats the purpose. The secret is in the formulation. For non-slip applications, installers mix in aggregates like quartz sand or aluminum oxide. This creates a textured profile that gives you excellent grip underfoot, much like the gritty surface of a skateboard deck.
- Real-World Example: An automotive repair garage needed a floor that could handle dropped tools, oil spills, and constant vehicle traffic. They chose an epoxy coating with a quartz aggregate. The benefit was twofold: the floor was durable enough to resist damage and the textured, oil-resistant surface provided secure footing for mechanics, even when dealing with lubricant spills, directly improving workshop safety.
Polyurethane Concrete: The Tough Defender
When your environment calls for the absolute highest level of durability, Polyurethane (PU) Concrete—also known as urethane cement—is the undisputed champion. This system blends the flexibility and chemical resistance of polyurethane with the raw strength of concrete. What you get is a floor that can withstand just about anything you can throw at it. Seriously.
PU concrete is built for extremes. It’s highly resistant to thermal shock (sudden, drastic temperature changes), aggressive chemicals, and heavy abrasion.
Real-World Example: A busy commercial food processing plant hits its floors daily with hot-water washdowns (thermal shock) and strong sanitizing chemicals. A standard epoxy might crack or peel under that assault. By choosing a PU concrete system, they created a seamless, non-porous floor that withstands this punishing routine without failing. This prevents bacterial growth in cracks and ensures they meet strict food safety standards, protecting both their employees and their product.
This image shows how different flooring types achieve their grip, from added textures in epoxy to the natural profile of other materials.
You can see how the aggregates in epoxy and the inherent texture of polyurethane create distinct surface profiles, which are key to preventing slips.
Polished Concrete: The Sleek Performer
Polished concrete takes a completely different path to slip resistance. Instead of adding a coating on top, this process involves grinding the concrete surface with progressively finer diamond abrasives until it reaches a smooth, high-gloss finish. Now, it might look slippery, but a properly polished concrete floor can meet and even exceed HSE standards for slip resistance.
The grip actually comes from the grinding process itself, which increases the floor’s Coefficient of Friction (COF). While it performs beautifully in dry conditions, its slip resistance can drop when it gets wet, making it a better choice for certain types of environments over others.
- Real-World Example: A large retail warehouse or "big-box" store needs a durable, low-maintenance floor that looks clean and professional. Polished concrete is an ideal fit. It handles heavy foot traffic and pallet jacks with ease, reflects light to create a brighter, more inviting space, and requires minimal upkeep. The direct benefit is lower long-term operational costs due to reduced cleaning needs and no need for periodic recoating.
Comparing Top Non Slip Industrial Flooring Options
To help you visualize how these options stack up, we've put together a simple comparison. This table breaks down the most common industrial flooring materials by their key performance factors, making it easier to see which one might be the best fit for your facility.
Flooring Type | Best For... | Durability | Chemical Resistance | Installation Cost |
---|---|---|---|---|
Epoxy Coating | Manufacturing plants, warehouses, garages, and workshops. | High impact resistance, good against abrasion. | Good, but can be vulnerable to certain acids. | Moderate |
PU Concrete | Food & beverage processing, chemical plants, and heavy industry. | Exceptional; withstands thermal shock and heavy abrasion. | Excellent; resistant to a wide range of harsh chemicals. | High |
Polished Concrete | Retail stores, showrooms, lobbies, and warehouses. | Very high for foot and light vehicle traffic. | Low; susceptible to acids and staining without a sealer. | Moderate to High |
Ultimately, the best non-slip industrial flooring is the one that's specifically engineered to solve your unique challenges. By understanding where each of these materials excels, you can make an informed choice that delivers lasting safety and performance.
While a permanent flooring system is a fantastic long-term investment, sometimes you need to address high-risk spots right away. For a closer look at more flexible solutions, check out our practical guide to anti-slip floor mats to see how you can improve safety in key zones immediately.
Auditing Your Facility for the Perfect Flooring Match
Choosing the right non slip industrial flooring isn't about picking the toughest or most expensive option off the shelf. It’s about finding the perfect match for your unique environment. The good news? You can become an expert on your own facility's needs long before you ever talk to a contractor.
Think of it like creating a detailed blueprint for your floor. By walking the floor and conducting a thorough audit, you can pinpoint the exact demands your operation places on it. This simple, proactive step ensures you invest in a solution that delivers lasting safety and performance, not just a temporary fix.
Your Actionable Facility Audit Checklist
To get started, grab a notepad and walk through your facility. Answering these questions will give you a rock-solid foundation for any conversation with a flooring professional, making sure you get a solution that fits your day-to-day reality.
- What kind of traffic does the floor handle? Is it mostly people on foot, or are you running heavy machinery like forklifts, pallet jacks, or scissor lifts? Actionable takeaway: Heavy machinery requires high impact resistance, pointing towards PU concrete or heavy-duty epoxy.
- What specific chemicals are used in the area? Make a detailed list of every cleaning agent, sanitizer, oil, and industrial solvent that might splash or spill onto the floor. Actionable takeaway: Frequent exposure to harsh acids or alkalis means PU concrete is likely the best choice for its superior chemical resistance.
- What are the temperature conditions? Does your floor have to put up with intense heat from ovens, sudden thermal shock from steam cleaning, or the freezing temperatures of a cold storage area? Actionable takeaway: Areas with thermal shock (e.g., hot water washdowns) immediately rule out most standard epoxies and point directly to PU concrete.
- What type of moisture is present? Are you dealing with constant water spills, or is the bigger issue oils, grease, or other slick substances? Actionable takeaway: Oily environments need a floor with both texture and oleophobicity (oil-repelling properties), a feature available in specialized epoxy and urethane systems.
Real-World Example: The manager of a busy brewery loading dock performed this audit. Their checklist showed: constant forklift traffic, frequent water spills from keg cleaning, and occasional splashes of caustic cleaning chemicals. This data made the choice clear. The benefit of the audit was that they could confidently specify a heavy-duty urethane cement system to contractors, knowing it met their exact needs for impact, moisture, and chemical resistance.
Understanding the Grip Rating: Coefficient of Friction
One of the key technical terms you’ll run into is the Coefficient of Friction (COF). Don't let the name intimidate you; it's just a fancy way of saying 'grip rating'. The higher the COF number, the more traction the surface has—and the lower the risk of slips.
The Health and Safety Executive (HSE) uses a PTV (Pendulum Test Value) to measure slip risk, but COF is also widely referenced. For most industrial settings, especially those with moisture or contaminants, you’ll want to aim for a high dynamic COF to guarantee safety.
- Static COF measures the force needed to get something to start moving from a standstill.
- Dynamic COF measures the force needed to keep something moving. This is often seen as a more realistic indicator of slip risk when people are actually walking or working.
Taking Action With Your Audit Results
Once your audit is complete and you have a handle on your COF requirements, you're in a powerful position to make an informed decision. This blueprint helps you choose between a full flooring system or more targeted solutions.
For instance, if your audit reveals that slip risks are concentrated in specific high-risk zones—like workstations or entryways—strategically placed matting might be a smarter, more cost-effective first step. To learn more about this approach, you can explore our resources on effective floor safety mats that tackle these localized hazards head-on.
Ultimately, this proactive audit empowers you to select the right non slip industrial flooring solution, ensuring your investment enhances safety, boosts productivity, and delivers real value for years to come.
Using Non-Slip Mats for Targeted Safety Solutions
A complete floor overhaul isn't always on the cards. Sometimes, what you really need is a flexible, targeted solution that gets you immediate results where it counts the most. This is exactly where non-slip industrial flooring mats come into play, becoming a critical part of your facility's safety playbook.
Think of mats as the special forces of your safety strategy. Instead of ripping up and replacing an entire floor, you can deploy them in specific high-risk zones for an instant impact. It’s a smart, cost-effective approach that lets you tackle problem areas with precision and speed.
Strategic Deployment for Maximum Impact
The real power of matting is in placing the right mat in the right spot. This isn't just about covering the floor; it's a targeted method that can dramatically improve safety and even boost productivity by neutralizing specific environmental challenges.
-
Real-World Example 1: Commercial Kitchens: A busy commercial kitchen is a constant battleground of water, grease, and food spills. Here, a combination anti-fatigue and drainage mat is a complete game-changer. The drainage holes let liquids fall through, keeping the surface workers stand on dry and grippy. At the same time, the cushioned build takes the strain off the legs and backs of chefs who are on their feet for hours, boosting both safety and comfort.
-
Real-World Example 2: Loading Docks: The loading dock is your facility's frontline against outside elements like dirt, rain, and snow. Placing a heavy-duty scraper mat here acts as your first line of defense. Its aggressive surface scrapes grime and moisture off shoes and cart wheels, trapping it right at the door before it gets tracked inside and turns the whole place into a slip hazard.
How to Implement This: Identify your top 3 risk zones (e.g., entrance, main walkway, a specific workstation). For each zone, choose a mat type that directly counters the primary hazard (e.g., scraper for entrance, drainage for wet area). This targeted approach provides an immediate safety boost for a fraction of the cost of a full floor replacement.
Choosing the Right Mat Material
A mat is only as good as the material it's made from. Each material brings its own unique strengths to the table, so matching it to the specific hazard you're facing is crucial. Getting this right is how you make smart, strategic decisions for your workplace.
Here’s a look at common mat materials and where they shine:
-
Rubber: Known for its incredible durability and fantastic grip, rubber is the go-to choice for high-traffic industrial areas. It has a natural slip resistance, even when wet, and offers a solid level of anti-fatigue support. It’s the perfect fit for manufacturing lines and workshops.
-
Nitrile Rubber: Think of this as rubber's tougher cousin. Nitrile gives you all the benefits of standard rubber but adds superior resistance to oils, grease, and chemicals. This makes nitrile mats the clear winner for commercial kitchens, auto repair shops, and any environment where chemical or oil spills are a daily reality.
-
Vinyl: Vinyl mats are often lighter and more budget-friendly, making them a great pick for commercial, retail, or office settings with less extreme conditions. They're excellent for providing anti-fatigue comfort at standing desks or checkout counters and offer reliable slip resistance in dry to moderately damp areas.
By understanding these options, you can roll out a targeted matting strategy that delivers an immediate, effective, and budget-friendly upgrade to your facility’s safety. This flexible approach to non-slip industrial flooring lets you strengthen your defenses exactly where they matter most.
Installation and Maintenance for Lasting Performance
So, you’ve invested in a top-tier non slip industrial flooring system. That’s a huge step toward creating a safer, more productive facility. But here’s the thing: even the most robust floor will fail if it’s not put down right and taken care of properly. Protecting that investment is what ensures it pays you back for years to come, keeping both your people and your bottom line safe.
Think of it like laying the foundation for a skyscraper. If the groundwork is shaky, the whole building is compromised. It’s the exact same with your floor—its entire performance hinges on how well the concrete underneath is prepared.
The Critical Role of Surface Preparation
Let’s be clear: proper surface preparation is non-negotiable for a floor coating that actually lasts. Your new system needs a clean, sound, and properly profiled concrete slab to grab onto. Without that powerful mechanical bond, you’re just asking for trouble—peeling, bubbling, and total failure that wastes every penny you spent.
To get that perfect surface, professional installers will typically use one of two heavy-duty methods:
- Diamond Grinding: This involves using massive industrial grinders fitted with diamond-impregnated discs. They grind away old coatings, contaminants, and the smooth top layer of the concrete, leaving behind a textured, porous surface that’s thirsty to absorb the new flooring system.
- Shot Blasting: This is the more aggressive approach. It fires tiny steel beads at the concrete at an incredibly high velocity. It’s perfect for creating a much deeper profile, which is exactly what you need for heavy-duty systems like polyurethane concrete.
Real-World Example: A food distribution warehouse decided to get a new epoxy floor to handle constant spills and forklift traffic. Trying to cut corners, they had their own team prep the concrete with a simple acid etch. Big mistake. Within six months, hot-tire pickup from the forklifts was ripping up huge sections of the coating, creating dangerous new trip hazards. The benefit of hiring a professional installer who used diamond grinding from the start would have been a floor that lasted its full 10-year lifespan, avoiding a costly re-installation.
An Actionable Maintenance Plan for Your Team
Once your non slip industrial flooring is beautifully installed, a consistent maintenance routine is the key to keeping it that way. Think about it: abrasive dirt and grit are like sandpaper under every footstep and wheel, slowly grinding down the very texture designed to keep your team safe. A simple, structured cleaning plan is all it takes to stop this damage in its tracks.
Here’s a straightforward daily, weekly, and monthly schedule you can hand right to your cleaning crew to protect your asset.
The 'Daily, Weekly, Monthly' Care Plan
1. Daily Tasks (The Sweep and Spot-Clean):
- Action: At the end of every shift, have someone sweep up all the loose dirt, debris, and dust with a soft-bristled broom or a dust mop.
- Why It Matters: This simple step prevents the daily grind of foot and vehicle traffic from turning tiny particles into an abrasive force that literally erodes the floor's non-slip texture. Any spills should be spot-cleaned immediately with a pH-neutral cleaner to stop stains or chemical damage before they set in.
2. Weekly Tasks (The Deep Clean):
- Action: Give the floor a thorough cleaning with a mechanical auto-scrubber using a non-abrasive pad or brush. Stick to a manufacturer-recommended, pH-neutral cleaner.
- Why It Matters: Harsh, acidic, or highly alkaline cleaners are your floor’s enemy. They can chemically attack the resin, making it brittle or discolored over time. A pH-neutral solution gets the floor sparkling clean without causing any harm, preserving the coating's integrity.
3. Monthly Tasks (The Inspection):
- Action: Walk the entire floor and give it a detailed visual inspection. Get down close and look for any signs of excessive wear, deep scratches, chips, or any areas where the coating might be lifting or peeling.
- Why It Matters: Catching a small chip early means a simple, cheap touch-up. But if you ignore it, you’re letting moisture and chemicals seep underneath the coating. That small issue can quickly become a massive failure that requires a major, expensive repair.
This kind of consistent care isn’t just good practice; it's smart business, especially in a rapidly growing market. The global industrial flooring sector was valued at around $10.05 billion in 2025 and is on track to hit $14.83 billion by 2032. With North America holding a massive 38.3% of this market, it’s clear how vital these floors are to modern industry. You can discover more about the industrial flooring market on coherentmarketinsights.com. By protecting your floor, you’re not just cleaning; you’re preserving a critical piece of your facility’s infrastructure and safety program.
Common Questions About Non Slip Industrial Flooring
Even after doing your homework and auditing your facility, it's natural to have a few practical questions. Investing in your facility’s flooring is a major decision, and you need to be completely confident before you commit. We get it.
This section tackles the most common questions we hear from facility managers and business owners just like you. Our goal is to give you direct, straightforward answers to clear up any final uncertainties, helping you move forward with the right choice for your crew, your operations, and your budget.
How Long Does Non Slip Industrial Flooring Typically Last?
The lifespan of your floor really boils down to three things: the material you choose, how well it was installed, and the daily grind it goes through. While there’s no single magic number, we can give you some solid estimates based on the type of system.
A professionally installed epoxy floor in a medium-traffic warehouse or workshop can realistically last 7-10 years. But if you step up to a more robust system like polyurethane (PU) concrete, which is built for the harshest conditions, you could easily see 20 years or more with proper care.
Real-World Example: A manufacturing plant has two identical work areas. Area A uses a cheap floor paint, replaced every 2 years. Area B has a 15-year-old PU concrete floor that is still performing perfectly. While the initial cost for Area B was higher, the benefit is a significantly lower total cost of ownership over the long term, plus zero downtime for floor replacements.
Can I Install New Flooring Over My Existing Concrete?
Yes, in most situations, you absolutely can. Modern non slip industrial flooring systems are designed to be applied directly over an existing concrete slab. The big "but" here is that the concrete underneath has to be properly prepared. You can't just paint over a damaged or dirty surface and expect it to hold up.
The concrete foundation must be clean, totally dry, and structurally sound. Any professional installer worth their salt will start by mechanically preparing the surface, usually through diamond grinding or shot blasting. This process strips away old coatings and etches the surface, creating a rough profile for the new system to grip onto—much like sanding wood before you paint it. Any significant cracks or damage have to be repaired first to guarantee a smooth, tough, and long-lasting finish.
What Is the Difference Between Anti-Slip and Non-Slip?
This is a really common point of confusion, but the answer is surprisingly simple. In the flooring industry, the terms "anti-slip" and "non-slip" are used completely interchangeably. There's no official technical or regulatory difference between them. Both phrases are just ways of describing a surface engineered to give you better traction and reduce the risk of slip-and-fall accidents.
Instead of getting hung up on the terminology, you should focus on the product's certified performance data. The number that truly matters is its Coefficient of Friction (COF) rating. This is the tested, verified measurement of its slip resistance and the real indicator of how safe it will be in your specific environment.
How Much Does Non Slip Industrial Flooring Cost?
The cost of a permanent flooring solution can vary quite a bit depending on the system you choose, the size of the area, and how much prep work is needed. A standard epoxy coating might run anywhere from $4 to $8 per square foot. For a heavy-duty system like PU concrete, you could be looking at $10 to $15 per square foot, or even more.
Don't forget that surface preparation is a major factor in that final price. While the upfront investment for a permanent flooring system can seem steep, it’s often far more cost-effective in the long run than repeatedly replacing cheaper, temporary fixes like paint or low-quality mats, especially in large industrial spaces.
For a closer look at how strategic matting can complement your permanent flooring, you can learn more about the benefits of targeted industrial non-slip mats in our detailed guide.
Ready to enhance your facility's safety with a targeted and effective solution? Explore the wide range of high-performance matting options at Mats4U. From heavy-duty entrance mats to specialized anti-fatigue and drainage solutions, we have the right product to solve your specific safety challenges. Visit us at https://www.mats4u.com to find the perfect mat for your needs.
Prev post
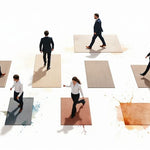
7 Best High Traffic Mats for Businesses in 2025
Updated on 20 July 2025
Next post

How to Boost Safety & Productivity with Industrial Non-Slip Mats
Updated on 18 July 2025